Most rubbers are a complex blend of materials. For car tires and footwear the best performing rubbers combine both synthetic and natural rubber. An unfortunate hurdle for achieving fully bio-based elastomeric materials
At least that was what I thought until I heard from Thomas Baumgarten. His company, Reselo has created a new, sustainable rubber from birch trees that has the potential to replace synthetic rubber, providing a much needed stepping stone to 100% bio-based rubber that is high performance and renewable.
The company was born from the realization that a family of molecules in birch bark, collectively called suberin, could be extracted and reformed into a material akin to rubber. It is a natural elastomeric material, but unlike natural rubber, it can be engineered to replace synthetic rubbers in many applications.
Here is the conversation with Dr. Baumgarten. It has been edited for clarity and brevity.
Aaron Nesser: Can you start by telling us a little bit about your background and how you got into materials science?
Thomas Baumgarten: I'm a biochemist by training. I studied in Germany and then moved to Sweden for my PhD. I started working with bacteria to produce proteins, but wanted to shift my career, and found a postdoc position with KTH at the Wallenberg Wood Science Center. There, research focused on biomass valorization, basically asking what new things can we do with trees?
It’s motivated by the forestry industry which is huge in Sweden and there is a strong sense that paper is not a product for the future, so there is a general awareness that new products need to be developed from renewable resources like trees.
AN: So your work is part of a fundamental shift away from paper that still leverages trees and forests.
TB: Yes, paper is useful today but biomaterials are the future since they have a higher value. With society phasing out fossil resources, fossil-based materials like plastics and rubbers need to be replaced eventually. Here lies a huge opportunity, both in terms of capturing economic value but also contributing to establish a sustainable bioeconomy. However, to reach the scale needed we have to start now. Stora Enso is leading the way — I think about ⅓ of their revenue already comes from biomaterials. They have been innovating around lignin, including lignin-based adhesives and batteries. They are already starting to pilot and scale some of these technologies and they really work.
One of the wake-up moments for me was seeing researchers excited about plastic with 30% cellulose content. It was celebrated as an achievement, but it seemed backwards to me. Why spend 3-4 years of research just to make plastic with wood mixed in.
AN: Totally – I still see designers taking a bio-based material, encasing it in plastic or resin and calling it a biomaterial. That is not innovation and is really the opposite of what we need to be doing in design and material science.
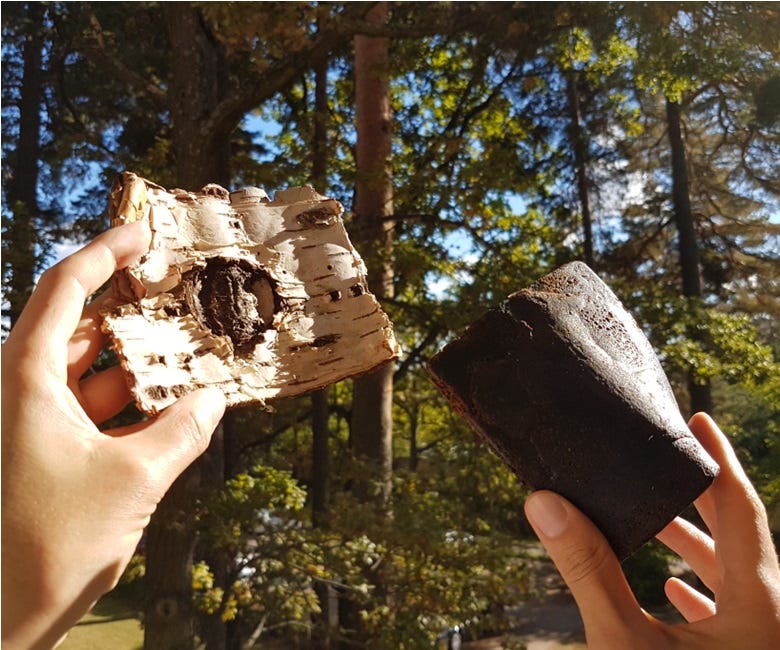
How to make rubber from birch bark
AN: Can you tell me about how you started making rubber from birch bark?
TB: At WWSC I was very free to explore. I first worked with enzymes, which didn’t really work out, so I shifted to organic chemistry to take birch bark, separate its polymers, and then put them back together in a certain way. And that's how I first made this rubber material.
AN: Can you tell me about the process and why birch bark specifically?
TB: Birch bark has a unique composition – it actually has very few main components. Spruce or Pine for example has 40+ chemicals and separating them is an expensive process that doesn’t scale.
In birch bark you have 3 main components: betulin, which is already used in cosmetics and food supplements, lignin carbohydrates, which has been considered a waste product and is often burned as an energy source. And then there's suberin, which is a network of long-chain fatty acids that makes birch bark flexible. This is what we’re interested in. We extract the suberin, break it down to its monomer, and put it back together in a test tube to get a rubber material.
AN: Wow, so how much suberin is actually in the bark?
TB: A good sample of birch bark can have 30–40% suberin. These are levels that can actually support a cost-competitive industrial process.
AN: That's really a lot. 30–40% of a single chemical from a plant is kind of wild.
TB: Yes. Achieving these yields is part of our core innovation. Suberin comes in different sizes from C16 up to C24 [this refers to carbon chain length]. Conventional thinking would have us extract each compound individually, but If we do that, the yield for each drops to 1% or below for each compound. If we extract them all together, our yields are very high.
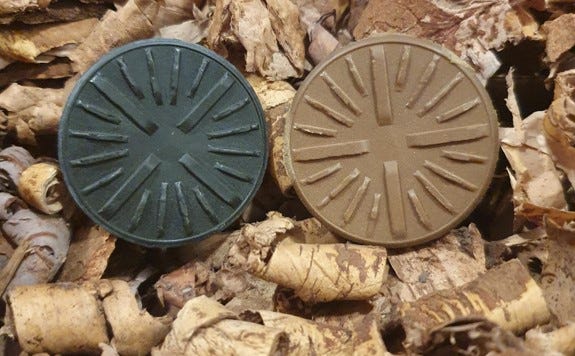
Materials are complex, but they don’t have to be difficult
AN: So, you're saying that if we want to make materials from nature, we have to take whatever is there and work with it.
TB: Exactly. That's what people did in the past, right? Before they had fancy chemistry, they took what was there – natural rubber is a great example – and worked with it. There's very little processing of natural rubber after harvest. It's a complex mixture, but it works.
AN: Can you explain how natural rubber is harvested and produced?
TB: Yeah, it's essentially just tree sap. You extract it, dry it, and maybe smoke it. That's it.
AN: Is your material similar to natural rubber aka isoprene?
TB: No, our material is not isoprene. Because it’s made from fatty acids it is technically a type of polyester. It has a completely different chemistry compared to almost all rubbers available today, but it works. It is natural, it is rubber, but it’s not isoprene.
AN: How does it perform? Talk to me as a shoe designer.
TB: If you make shoes nowadays, you’ll work with rubber recipes that combine rubber polymers, fillers, and additives. Our material fits into this same structure, but you need to develop new recipes. You can start from 100% Reselo Rubber or mix it into existing recipes to replace fossil-derived polymers and thus decrease the carbon footprint.
With any rubber, natural or synthetic, mixing it with different rubbers, fillers, and additives gives you better performance, and it is the same with Reselo Rubber. Performance is about recipe development.
AN: So in instances where a natural rubber would be mixed with a synthetic rubber, you are replacing the synthetic rubber with birch tree rubber to create a more natural and renewable material.
TB: Exactly. We want to phase out fossil resources, and this is a pragmatic approach to get there. We are not trying to replace the whole ecosystem.
AN: What about biodegradability?
TB: That's not a focus yet. We believe our material should be more biodegradable due to its chemical structure, but it's a complex challenge. We don't want shoes or tires to lose performance quickly, but we also don't want microplastics accumulating in nature.
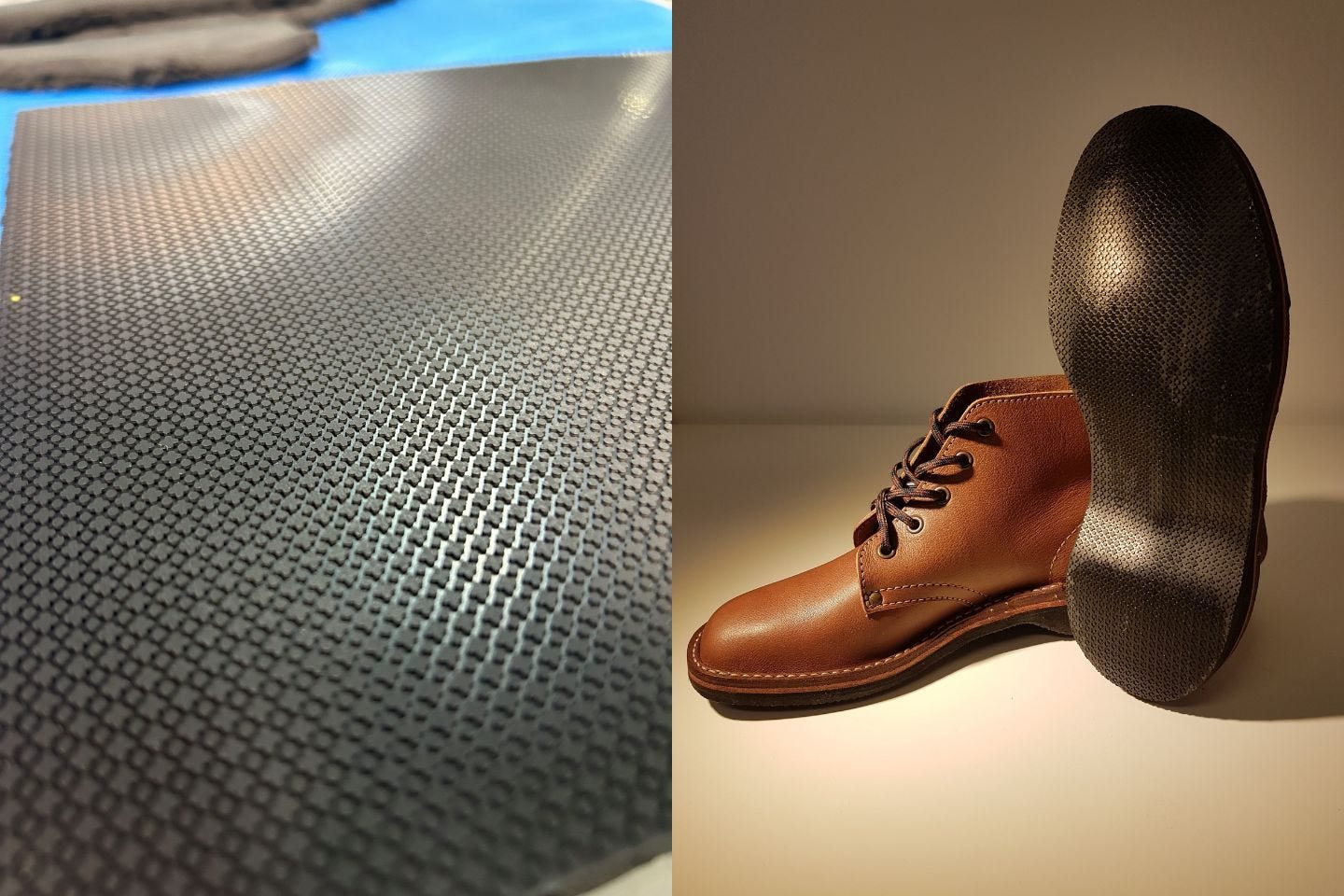
The next 50 years
AN: What do you see as the most important challenge for the rubber industry?
TB: Transparency is key. Today the industry lacks meaningful carbon footprint data, and the missing piece is supply chain transparency. The regulations to change this are coming, and it will mean that companies are punished if they use high carbon footprint materials, and customers will pay more.
This is going to be felt the hardest in the synthetic rubber industry. The leading companies have not even begun to ask what kind of carbon footprints their materials have, and when they do it will be very hard for them to trace all of their supply chains.
AN: So is natural rubber a good bio-material, renewable and sustainable?
TB: Yes, but the way we produce it is completely wrong. Like palm oil and other plantations, it's not sustainably managed. That said, there has been a lot of progress around transparency and sustainably managed forests.
AN: Is there a shoe made entirely from trees in the future?
TB: Yes, some designs are close. For example, Birkenstock uses cork in their shoes, and the main part is mostly biobased, except for the EVA foam in the outer sole. Replacing synthetic polymers in rubber is the first big step forward for footwear.